

caisson
technology
technology
harbor technology
/green technology




- Mud pressurization (DK) shield method
- Double-O-Tube (DOT) shield method
- Developing Parallel Link Excavation (DPLEX) shield method
- Jack-driven Developing Parallel Link Excavation (J-DPLEX) shield method
- Detaching And Proceeding to dig Piping (DAPPI) construction method
- Mud pressurizing propulsion method




History of pneumatic caisson
This page introduces the history of the pneumatic caisson, which triggered the foundation of Daiho Corporation.
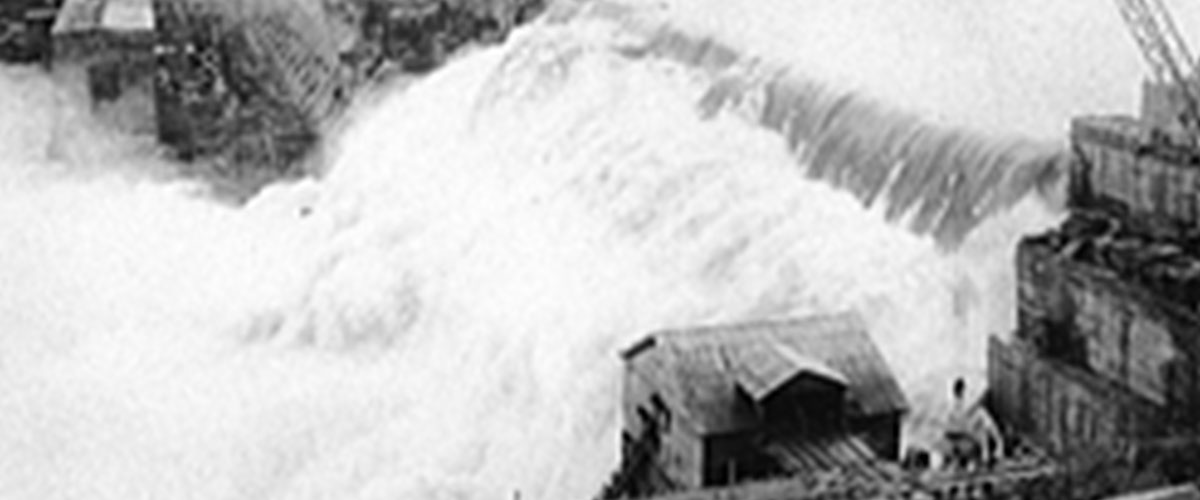
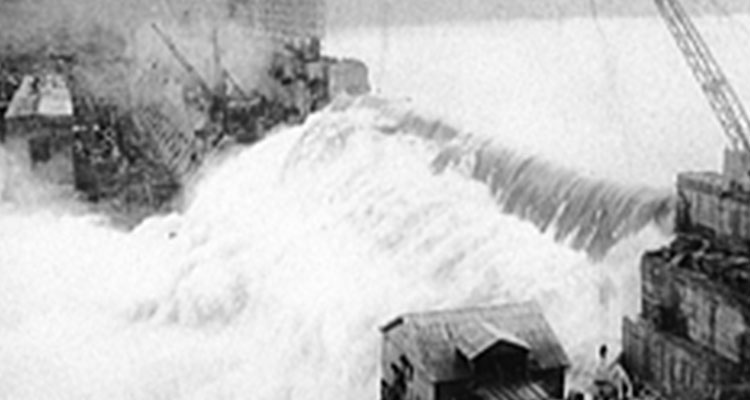
Born in France in 1841
It is said that the world’s first ground excavation utilizing air pressure was excavation/go down using iron pipes on the sand bank of Loire River in France, conducted by M. Triger in 1841. In this work, M. Triger, who invented the air lock, covered the approximately 1m iron-made cylindrical foundation built on the ground with an air lock, sent compressed air into the tube to eliminate filled water, and then, the operator climbed down to the tube bottom and succeeded in excavating/sinking up to approximately 20 m below the surface. This is said to be the original pneumatic caisson method, which then spread across Europe and entered the U.S., where the method has evolved independently.
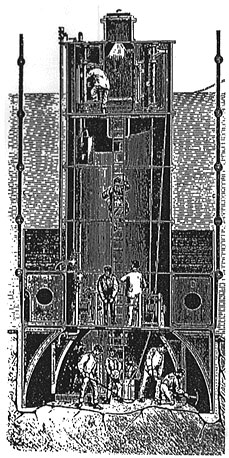
This is said to be the original form of the pneumatic caisson method, which was then spread across Europe and introduced into the United States, where the method has evolved independently. The world’s first foundation work using the pneumatic method was the pneumatic pile adopted for a bridge pier foundation near Rochester, U.K., in 1851. From then on, this construction method has evolved into pneumatic caisson, and in the late 19th century, it was adopted for the foundation of the Brooklyn Bridge and St. Louis Bridge in the U.S., the Forth Bridge in the U.K., the Eiffel Tower in Paris (2 among 4 piers facing Seine River), and so on. Then, iron-made caisson was gradually replaced by stone masonry, which had weak tensile force so people stopped using it. Meanwhile, in the U.S. where wood materials are abundant, wooden caisson was used for economic reasons, however, walls bend due to wood drying in compressed air, thus air leaks easily, and stress is unevenly applied during sinking, running the risk of problems and fire. As such, wooden caisson gradually fell into disuse. The pneumatic caisson was adopted also for many skyscrapers that were built in downtown New York in the beginning of the 20th century. Excavation work was fully manual at that time, and there were various issues concerning the work, including decompression disease often occurring due to a lack of knowledge. Furthermore, worker wages at that time were pretty high, reflecting the severe working environment, meaning it was an inefficient and expensive construction method highly dependent on manual work. For reference, measures against decompression disease were first considered around 1910, after more than 1,000 people had suffered from it. However, since there was no construction method for large-scale underground structures, this construction method was actively used in Europe and the U.S. and technological development continued until around 1930s. In Japan, the technology was introduced from the U.S. as part of the earthquake recovery project after the Great Kanto Earthquake in 1923, and it was adopted for new establishment work of the destroyed Eitai Bridge, Kiyosu Bridge, and Kototoi Bridge. Afterwards, development of steel products and construction machines progressed in the U.S. and European countries except for Germany, and when new construction methods such as long and massive steel piles and open caisson were developed, this expensive pneumatic caisson method with severe working conditions came to be disliked, and all at once it almost stopped being used during the 1930s, and this trend has continued. Conversely, in Japan and Germany, pneumatic caisson was steadily used even during World War II. As both countries were in the middle of a hopeless war, they could not afford to assign important resources such as steel materials to anything other than military purposes, especially in Japan, and they didn't have the capabilities to develop new construction methods using lots of steel materials that are superior to pneumatic caisson.
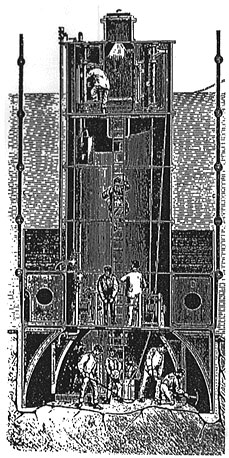
“Daiho’s Pneumatic Caisson
Construction Method” was
born during the construction of
Homan Dam
In 1936, Homan Dam was constructed on Second Songhua River of former Manchuria (river width: 700 m to 800 m). This huge gravity dam was 1,200 m in length, 91m in height, and 220 m3 in volume, making it the second largest dam in the world at that time. Although the preliminary shuttering work was initiated on the left bank in 1939, underwater concrete work in severe coldness was extremely difficult, and obstacles such as gabions and cobblestones froze in the bottom of the river connecting to the right coffering bank, which could not be easily removed. To solve this, an idea was born: sinking the “simplified pneumatic caisson” in the river bottom to remove obstacles, making it contact the rocks, and placing concrete at the bottom to make it part of the cutoff wall. For this caisson, another slab was added above the workroom of normal pneumatic caisson to form an airlock room, allowing safe and comfortable underwater excavation work. This has become the basis of “Daiho’s Pneumatic Caisson Method”, which was established in later years. Then, members involved with the Homan Dam founded Daiho Corporation in 1949. In the “Recovery Work for Adjacent River Bank of Owatari Bridge”, “Daiho’s Pneumatic Caisson Method”, involving the transport of excavated soil and pressurization/depressurization work conducted by airlock installed in the reinforced concrete double slab structure, was proposed and adopted for the first time after the war. In December 1951, the patent was obtained for “Daiho’s Pneumatic Caisson Method”, as the “construction method for building concrete structures in the bottom layer or spring layer” (Patent: No.193732 filed on Jan 30,1951).
Homan Dam
Cutoff wall work on the left shuttering bank using pneumatic caisson method
Realizing high efficiency
and low price through Daiho Corporation’s
technological development
Upon entering the age of high economic growth after WWII, and looking ahead to the 1964 Tokyo Olympics, extensive investment was made in construction such as the Tokaido Shinkansen and highway maintenance. From 1962, due to the introduction and dissemination of large-diameter cast-in-place pile methods such as the benoto pile method, the reverse circulation method and the continuous underground wall method in Japan, the application field of pneumatic caisson method was threatened, resulting in the reduction of needs. However, unlike the U.S. and Europe, this method never disappeared in Japan. This is because of vigorous technological development conducted to make it a highly efficient low-price method, the realization of introducing machines for excavation work in the compressed air workroom (ceiling travel-type excavator, etc.), the establishment of a rational design method for caisson foundation structure, technological innovation such as unmanned technology for main work through remote operation, and cost reduction.
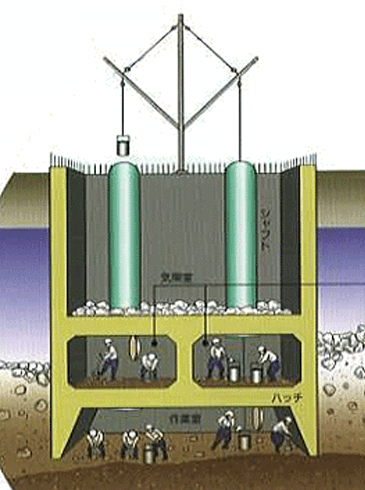
Earthquake resistance
and raising hopes for
various applications
At the time of the Niigata Earthquake in 1964, the Bandai Bridge, which adopted the pneumatic caisson method, was hardly damaged, and in the Great Hanshin Earthquake on January 17, 1995, structures built using the pneumatic caisson method were hardly damaged. This caused caisson to attract more attention as a structure more resistant to earthquake than expected. For a while, adoption decreased as the steel lock that can be conveniently installed on site became popular due to the reduction of steel materials, but recently, thanks to the increased depth of pneumatic caisson and increased large-scale caisson work, the need for work safety, work environment improvement, and cost reduction increased, and the double slab was revived and adopted again for the foundation of Rainbow Bridge from 1987 to 1990. From then on, for Mabechi Bridge (substructure) work on the Tohoku Jukan Expressway constructed from 1997 to 1999, the conventional Daiho pneumatic caisson method was renewed, and the new Daiho pneumatic caisson method (current New DREAM construction method) was adopted combining newly developed in-house technology. It is currently used for bridge foundation, pump sites related to rainwater storage facilities, departure shaft, etc.
Examination certification /
patents / awards
- Registered in New Technology Information System (NETIS)
- ・DREAM construction method, New DREAM construction method
(NETIS number: (original) KT-990343-VE)
- Theme Setting Technology Application System of the Ministry of Land, Infrastructure, Transport and Tourism (FY 2003)
- ・Revolutionary technology in the construction field (DREAM construction method)
- New technology and research achievement certificate
- ・Japan Institute of Wastewater Engineering and Technology Research on construction of rainwater storage facility by unmanned pneumatic caisson method (No. 19003)
- Patent list of pneumatic caissons (excerpt)
- ・Pneumatic caissons (Caissons having a maintenance room for excavation machine using double slab) (Patent: No.3470894 filed on Dec.3,2001)
- ・Test method of bearing power of soil and device used (attached to the excavator and remotely controlled) (Patent: No.2747896 filed on Nov.9,1995)
- ・Caisson (multi-room double slab)
(Patent: No.3349974 filed on Dec.28,1998)
- JSCE Award Tanaka Award Work Division
-
Fiscal 1993 Rainbow Bridge1993 Higashi Kobe Bridge1998 Shiratori Bridge2003 Kitakami Bridge2008 Yabe River Bridge2017 Onahama Marine Bridge