

caisson
technology
technology
harbor technology
/green technology




- Mud pressurization (DK) shield method
- Double-O-Tube (DOT) shield method
- Developing Parallel Link Excavation (DPLEX) shield method
- Jack-driven Developing Parallel Link Excavation (J-DPLEX) shield method
- Detaching And Proceeding to dig Piping (DAPPI) construction method
- Mud pressurizing propulsion method




New DREAM Construction Method
The new pneumatic caisson method built with the concept of combining unmanned technology for work under high pressure and safety technology according to the work conditions.
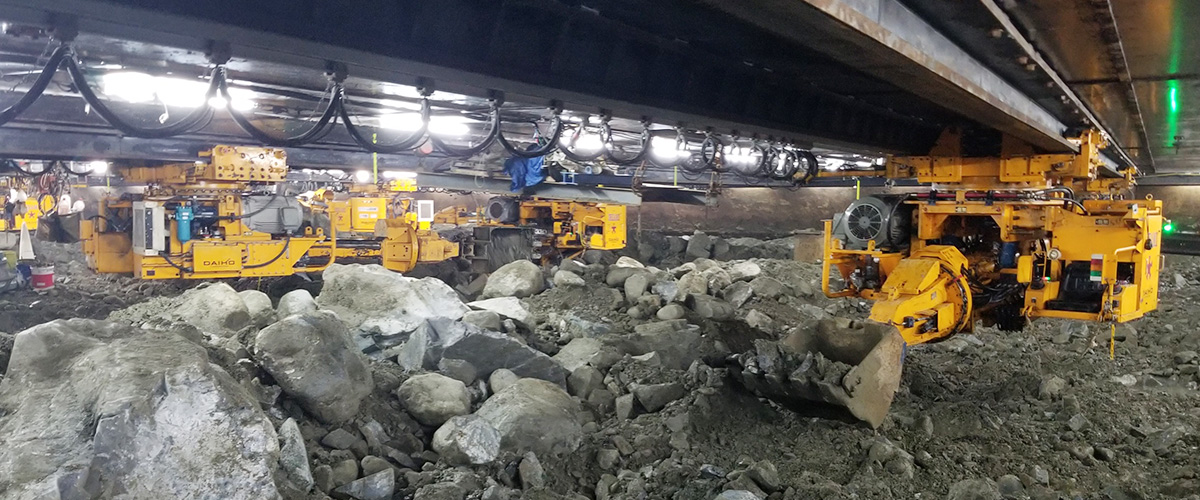
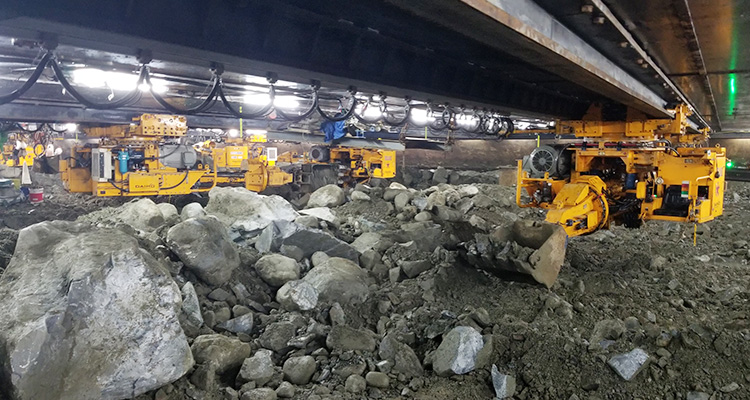
Outline of New DREAM
Construction Method
The New DREAM construction method is a new pneumatic caisson method built with the concept of combining unmanned technology for work under high pressure and safety technology according to the work conditions. This construction method allows for improvement of a great deal of work efficiency and safety of the pneumatic caisson method, and especially when it is equipped with an excavator maintenance system, realizes fully unmanned operation. This contributes cost reduction, improved safety, and shortened work period.
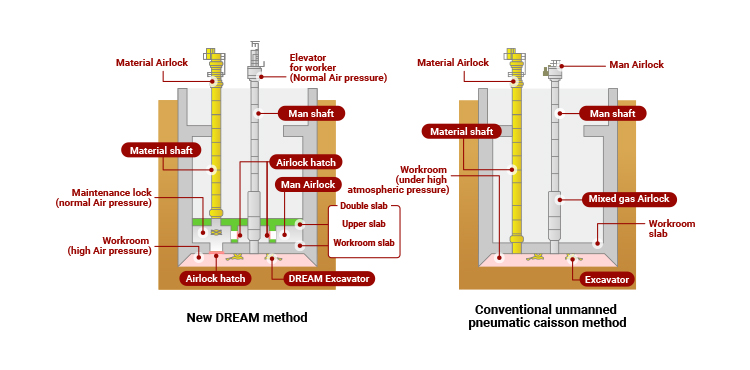
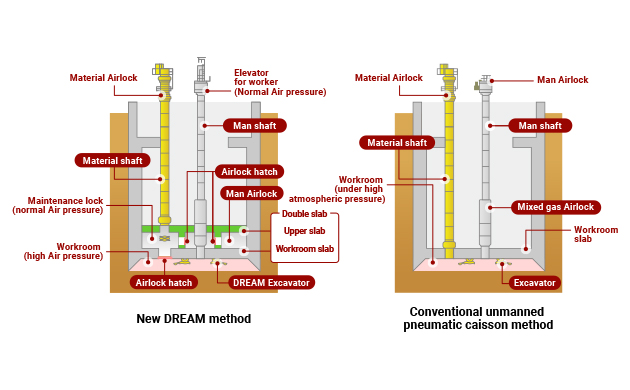
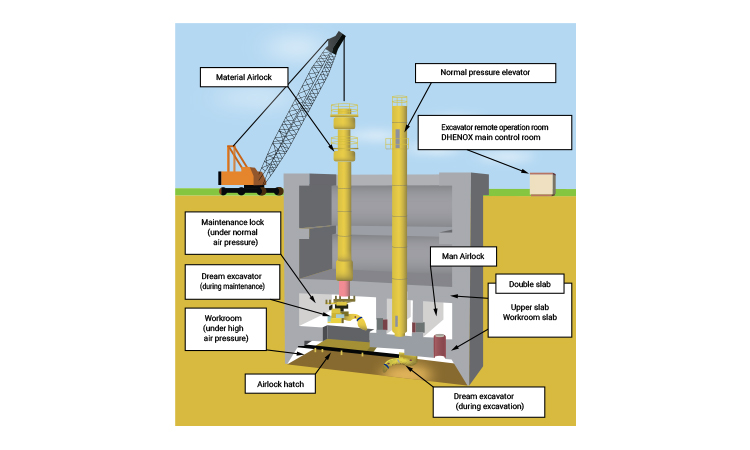
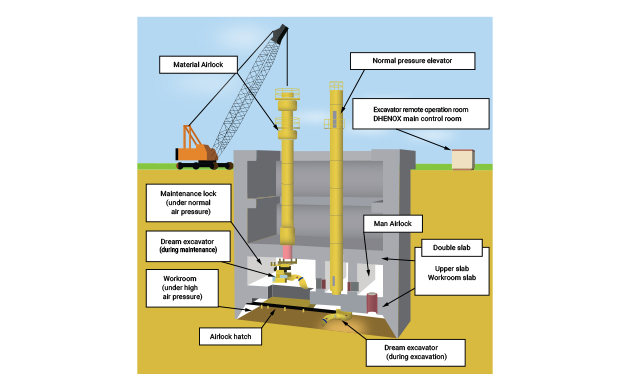
Characteristics of New DREAM
Construction Method
1. 100% unmanned work under high pressure
Daily inspection/maintenance and recovery work is conducted by maintenance airlock under atmospheric pressure, and soil bearing power is tested through remote operation, therefore, work under high pressure is very few, allowing for 100% unmanned work under high pressure.
2. Zero occurrence of hyperbaric disorder
Since work under high pressure is conducted only in emergencies, occurrence of decompression sickness can be reduced greatly.
3. Improvement of work environment
Since work under high pressure as well as the use of helium-containing gas is greatly reduced, it results in much less physical burden to operators, ensuring safety.
4. Cost reduction by approximately 10%
Thanks to the small-sized helium-containing gas equipment used to deal with high depth, part of daily inspection/repair work as well as recovery work, etc. is conducted under atmospheric pressure, therefore, good work efficiency is ensured and costs can be reduced.
5. Drastically shortened excavation process
Since daily inspection/maintenance and recovery work of excavator can be conducted under atmospheric pressure, there is no restriction for the work time.
6. Capable of work at high depth (water depth 70 m)
The fully unmanned work in the high-pressure room enables installation of caisson at high depth.
Unmanned New DREAM
Construction Method Technology
Since excavation work is remotely operated from above the ground, workers are free from high pressure and can safely conduct excavation work. Compared to the conventional machines, output is 2.5 times higher at maximum (15kw→37kw) and bucket capacity is 2 times at maximum (0.15→0.3m3), therefore, the excavation process can be shortened dramatically. The multi-functional caisson excavator can excavate normal soil to rocks (160MPa) by attaching a bucket or a rock drill.
-
DREAM II excavator (bucket 0.3 m3)
-
DREAM II excavator Breaker (300 kg class)
-
DREAM II excavator Drifter (350 kg class)
-
Remote operation from the ground (free from high pressure)
With a newly developed traveling system, which remotely operates the movement of excavator between the workroom and maintenance airlock, daily inspection/maintenance, as well as repair/disassembly/recovery work can be conducted at atmospheric pressure; therefore, work under high pressure can be eliminated. This leads to cost reductions, contributes to improving the work environment, and prevents a hyperbaric disorder.
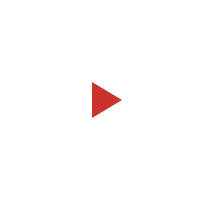
By using a device for testing the bearing power of soil by remote operation, installation, measurement, and removal of the testing device is performed from the ground through remote operation, therefore, work under high pressure associated with the soil bearing power test is not required.
-
Device for testing the bearing power of soil by remote operation
Our Works
-
- Facility name
- Shafts of Shonan Road
- Construction Technology
- Shield departure shaft
- Construction site
- Kanagawa Prefecture
- Client
- Ministry of Land, Infrastructure, Transport and Tourism